Uncompromising
quality
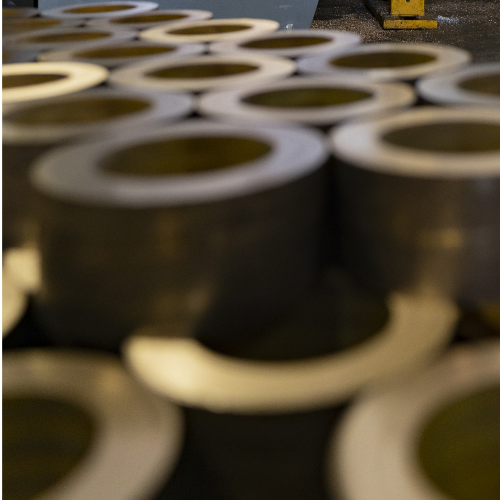
It starts with the best raw materials
From USA, UK, China, Germany and France, MASPRO scours the world for first-class suppliers of certified material including forgings, bar stock, extrusions, wire rope and engineering plastics.
Once received, the material undergoes pre-production testing to ensure it complies with the specifications and that its properties will perform in the required application.
“Before creating a part, we assess the required material composition and the manufacturing processes down to microscopic levels. Our analysis covers the specification of every element, down to case depth, profile plotting, and types of tempering. The analytics behind it are huge.”
Experienced metallurgists conduct chemical analysis with a spectrometer to confirm the composition. The materials are also magnified to undergo microstructure analysis to ensure they meet the specifications.
Each batch of metal will be granted a pre-manufacture certificate by the metallurgist confirming it is up to scratch.
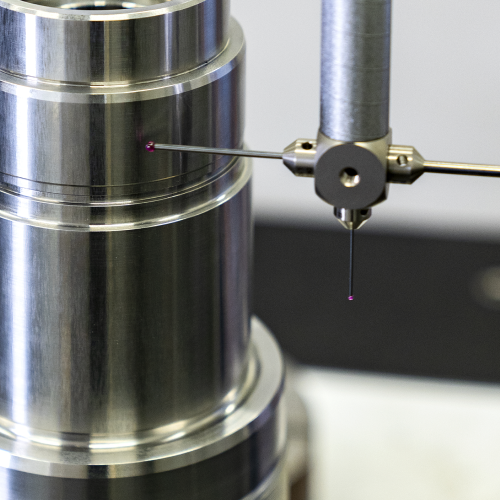
Precision manufacturing
From USA, UK, China, Germany and France, MASPRO scours the world for first-class suppliers of certified material including forgings, bar stock, extrusions, wire rope and engineering plastics.
Once received, the material undergoes pre-production testing to ensure it complies with the specifications and that its properties will perform in the required application.
“Before creating a part, we assess the required material composition and the manufacturing processes down to microscopic levels. Our analysis covers the specification of every element, down to case depth, profile plotting, and types of tempering. The analytics behind it are huge.”
Experienced metallurgists conduct chemical analysis with a spectrometer to confirm the composition. The materials are also magnified to undergo microstructure analysis to ensure they meet the specifications. From USA, UK, China, Germany and France, MASPRO scours the world for first-class suppliers of certified material including forgings, bar stock, extrusions, wire rope and engineering plastics.
Once received, the material undergoes pre-production testing to ensure it complies with the specifications and that its properties will perform in the required application.
“Before creating a part, we assess the required material composition and the manufacturing processes down to microscopic levels. Our analysis covers the specification of every element, down to case depth, profile plotting, and types of tempering. The analytics behind it are huge.”
Experienced metallurgists conduct chemical analysis with a spectrometer to confirm the composition. The materials are also magnified to undergo microstructure analysis to ensure they meet the specifications.
Each batch of metal will be granted a pre-manufacture certificate by the metallurgist confirming it is up to scratch.
Each batch of metal will be granted a pre-manufacture certificate by the metallurgist confirming it is up to scratch.
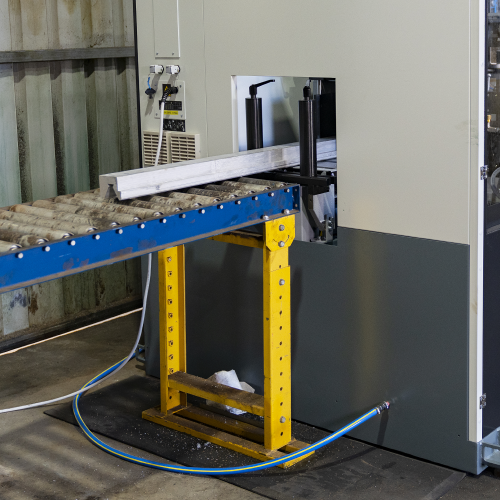
Identification and traceability
The manufacture of critical parts includes documented processes, formal certificates and verifiable reporting every step of the way. Parts are given a unique serial number and stamped so that everything is auditable, identifiable and traceable. This process conforms to ISO9001:2015.
Quality,
End-to end
approach
YOU CAN RELY ON MASPRO FOR YOUR SPARE PARTS NEEDS
If you’re managing procurement and thought you couldn’t find a dependable supplier with unbeatable quality, competitive pricing, strong in-stock position PLUS full technical and customer service support, think again.
Get in touch