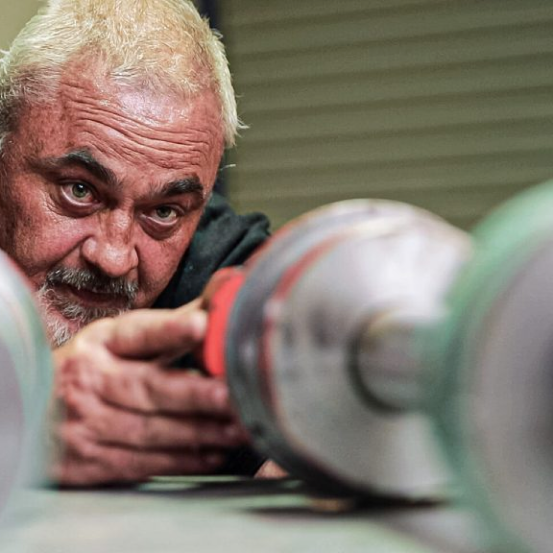
HOW REBUILDING PARTS IS SAVING MINES THOUSANDS
After seeing too many worn hydraulic cylinders being replaced with new ones unnecessarily, Product Support & Service Manager Mick Blunt was instrumental in helping MASPRO set up their dedicated rebuild facility in Parkes to help meet customers’ needs and lower their costs.
Just over 12 months later, as yet another truck rolls into the gantry full of parts for Mick to work his magic on, it’s fair to say the facility has proven a hit with clients. It’s not hard to see why.
Good as new for less
When we rebuild a hydraulic cylinder, we replace the consumable items with new ones and rebuild the part from scratch.
“For our clients, this means they get the same service life as a brand new part, typically for around 40-60% of the price. With high-value parts, that really adds up to a big saving,” explains Mick.
Here’s how it works:
- The first step is stripping each part down to analyse and identify sealware issues, wear patterns and any significant problems.
- All the components are sand blasted, honed and cleaned, before the part is rebuilt with new oil, seals and replacement fittings.
- Before testing, cylinders are left for at least 12 hours to ensure everything sets correctly.
- Next, it’s off to the hydraulic test beds for pressure variance testing.
- Finally they are cleaned, polished, painted and boxed up good as new.
Fixing the root of the problem
“When we get a broken hydraulic cylinder in to rebuild, the first thing we’ll do is a full inspection and diagnostics report to determine what’s gone wrong, what needs replacing and why it failed.”
The purpose of this is two-fold. Firstly it helps MASPRO determine exactly how to return this part to 100% performance. But even more importantly, it helps identify recurring faults that may be caused by maintenance issues, machinery problems or ill-fitting parts.
Mick sees this as a significant advantage over OEM manufacturers.
“A unique benefit of having our own rebuild workshop and manufacturing plant is our ability to not only diagnose repeat problems, but to then work with our engineers to redesign the part or the process to prevent it happening again so fast.
“This flexibility is not possible with OEM parts, which are all standard out of the main factory.”
Lifespan increased 400%, saves thousands of dollars
Mick explains an all-too-common scenario:
“Last year we had a client come to us with recurring cylinder failures well above normal wear and tear. By analysing the problem and slightly re-engineering the part specifications, we fixed the underlying issue.
“The adjusted parts increased the lifespan of each cylinder from 250 hours to over 1000 hours – and that’s on a $7,000 part each time! Not to mention all the other associated problems a broken part will cause in a mine in terms of down-time and wasted time ordering and replacing parts.”
Fixed cost repairs
With no middle man, and full control over the rebuild process in-house, MASPRO delivers quality products with fast turnarounds, and can offer fixed price repairs on many common cylinders.
“Pre-approved prices means we can get started as soon as we get the part – often turning it around as soon as the following week. Skipping the whole quote and approval phase can save a lot of time, especially if clients are rostered off at the mines.”
What’s next for the rebuild division?
Given the success so far, MASPRO and the team have plans to broaden the scope and potentially double production over the coming 18 months.
“Right now we’ve got a full schedule and demand is growing. To take the next step, we plan to invest in expanding the facility, separate the stripping and painting workshops and streamline some backend processes. A few more tradies in here would be nice too!
“It’s been a busy year. But busy is a good problem to have.”
Tour MASPRO’s Rebuild Facility
After seeing too many worn hydraulic cylinders being replaced with new ones unnecessarily, Product Support & Service Manager Mick Blunt was instrumental in helping MASPRO set up their dedicated rebuild facility in Parkes to help meet customers’ needs and lower their costs.
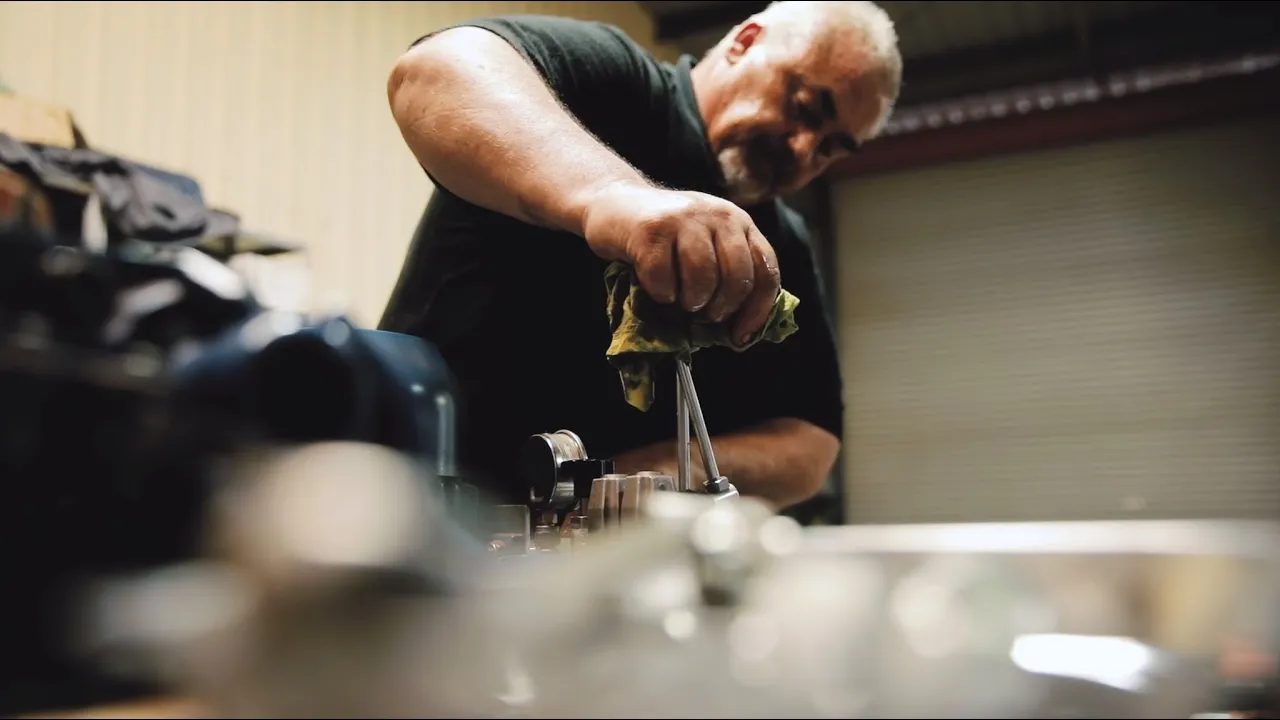
Streamline your mining parts processes
Get in touch with the experienced team at MASPRO
Get in touch